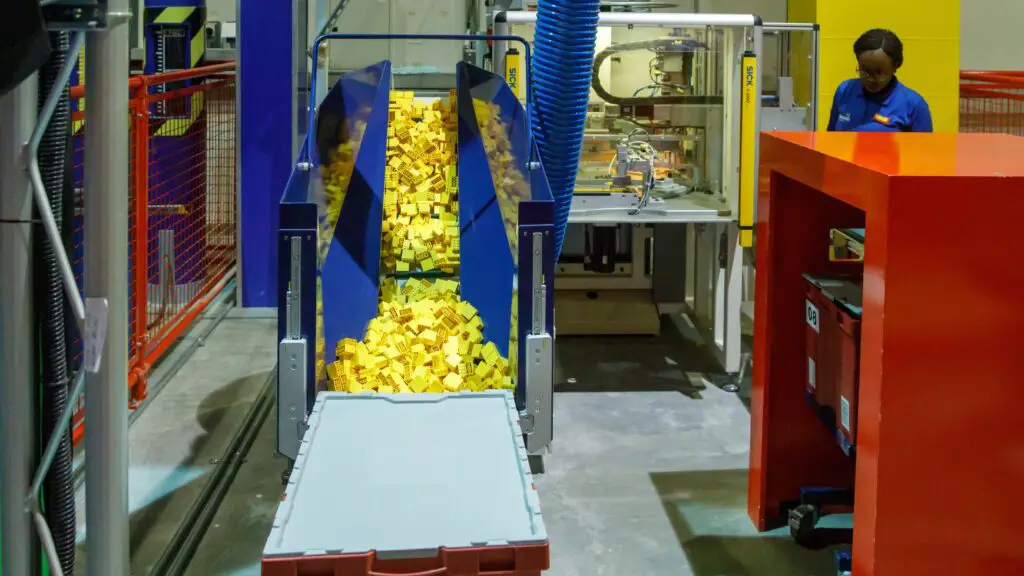
LEGO bricks are one of the world’s most beloved and iconic toys and have become a staple in many homes around the globe.
But have you ever wondered about how these vibrant, colorful blocks are made?
It is an incredibly complex process that requires a great deal of expertise, skill and dedication to ensure each and every piece meets high-quality standards.
Since 1949, LEGO bricks have been manufactured using a molding process. The molding process has not changed much since it was first invented, but there have been some updates over the years. In 1963, LEGO began using ABS plastic to make their bricks, which gave them a more consistent color and finish.
Table of Contents
How Are LEGO Bricks Made?
LEGO bricks are created through the process of injection molding. Raw plastic is mixed with colorants and fed into an injection molding machine. Injection molding involves heating thermoplastic resin until it becomes a liquid and forcing it under pressure into a steel or aluminum mold cavity in the shape of the desired product.
After cooling, the brick pieces are ejected, sorted and checked for quality before being packaged and shipped to retailers worldwide.
The production process is highly automated and precise, ensuring each brick meets exact specifications and can be combined with other LEGO pieces without issue.
Injection molding is one of the most cost-effective ways to quickly produce large numbers of identical pieces and with minimal waste material.
Furthermore, each color has a unique pigment combination that allows it to remain consistent over time.
This is why it has become one of the go-to methods for mass-producing items such as LEGO pieces over the years.
Other advantages include high levels of precision, low labor costs, and good material strength – because each piece is made in a single step, there’s no risk of human error or inconsistency between each part.
Additionally, this method can be used to produce parts with complex shapes and intricate details.
Making it ideal for producing components that might not be achievable through other manufacturing processes.
What Are LEGO Bricks Made Out Of?
LEGO bricks are made from a highly durable type of plastic called Acrylonitrile butadiene styrene (ABS) plastic.
ABS is a strong, lightweight thermoplastic with excellent impact resistance and shock absorption.
In other words, it is very resistant to wear and tear, making it suitable for use in the manufacturing of toys such as LEGO bricks, which experience significant handling during playtime.
Underneath the surface of each LEGO brick lies an intricate lattice structure that gives them their strength and stability.
This helps to ensure that the pieces fit together correctly and stay together even after considerable use or even accidental drops or knocks.
The unique construction technique used to create these tiny building blocks allows them to be assembled into large structures without compromising the integrity of any individual piece.
LEGO bricks come in a variety of colors thanks to their special injection molding process.
This enables designers to add vibrant pigments directly into the plastic material before it is formed into its distinctive shape.
This ensures that each component contains color throughout so that its hue remains consistent even after years of use or handling.
Additionally, every LEGO brick is crafted using high-quality standards and strict safety guidelines set by LEGO Group’s safety team.
Given their durability, versatility and quality construction, LEGO bricks have become a beloved pastime for kids all over the world.
Who enjoy constructing imaginative worlds through play with these tiny interlocking pieces.
How Are LEGO Bricks Made Step-By-Step?
Step 1: The production of LEGO bricks begins with the creation of raw plastic granulate pellets which are made from a variety of raw materials such as acrylonitrile butadiene styrene (ABS) and polyethylene.
These pellets are mixed with dye to give the LEGO bricks their color. There are over 50 colors used to color the bricks.
Step 2: The colored granulate is then led into molding machines that heat it to approximately 450 degrees Fahrenheit (230 degrees Celcius). The extreme temperature heats the plastic and melts it into a substance with a consistency like toothpaste.
Step 3: The toothpaste-like substance is then pushed into the mold with a tremendous pressure of 29,000 psi.
Step 4: The material is cooled within about 10 seconds and then ejected from the machine.
Step 5: The pieces are then sorted and plastic waste from the molds is ground and recycled immediately.
Step 6: Finally, LEGO elements must pass through extensive quality control processes before they can leave factories and enter shops around the world.
This involves testing every single brick against rigorous safety protocols and standards so that consumers get only high-quality products when shopping for LEGO products.
If a problem is detected during these tests, it is rectified before any further production takes place or those particular sets reach store shelves.
All the different elements are then automatically packaged into plastic bags and dropped into open LEGO retail boxes where instructions and large special elements are added by packing operators. Over 50,000 boxes are packed every 24 hours. The boxes are then automatically closed and sealed.
To find out how LEGO sets are actually designed, take a look at this article I wrote entitled “How are LEGO sets designed?”
The Molds
Each mold can produce one LEGO shape at a time. In order to make a different one, the Lego mold must be changed. Each factory has a department whose sole purpose is to maintain and clean the molds to ensure the best quality and precise brick is made.
The molds are always handled with great care to ensure that the highest quality is achieved so Lego bricks will always fit together perfectly. Each mold has specific instructions on time, heat and pressure.
Temperature and molding tests are always conducted to make sure the machine is programmed perfectly. These tests are examined by the quality department.
How Accurate Are LEGO Bricks When Produced?
LEGO bricks are known for their legendary accuracy and precision when produced.
Every single brick is molded with precision in mind, meaning each one fits perfectly together with the other pieces.
The accuracy of LEGO is due to its patented interlocking ridges, which allow it to remain strong despite being pulled apart or compressed.
Furthermore, LEGO has a tight tolerance rating of 0.005mm – one part of the brick can fit into any other brick within 0.005mm.
This means that even after many years of use and pulling apart, the parts stay snugly together without being loose or wobbly.
The accuracy and precision of LEGO parts also extend to colors and textures.
Since 2013, LEGO has used injection molding technology to precisely apply the colors and textures of the parts during manufacturing.
Ensuring each piece looks exactly as intended while still keeping its durability intact.
This type of technology also helps to maintain an even level of quality among various sets across different production batches.
To ensure its high standards are met every time, LEGO tests samples from every production batch before shipping them out from its factories around the world.
As a result, consumers can expect consistent quality from each set they purchase regardless of when it is made or where it was manufactured in.
This is especially true for licensed products such as Star Wars or Harry Potter sets that need intricate details replicated faithfully in order to be true to their themes.
Overall, LEGO bricks have been designed with unparalleled precision that has become synonymous with the brand over the decades since its creation in 1949.
This makes them ideal for creative play and for easily building complex models.
With such attention to detail taken on each piece during production, it is no wonder why these iconic blocks remain a beloved toy for children and adults alike all over the world today!
How Are LEGO Minifigures Made?
The process of making Minifigures is completely automated and begins with thousands of blank heads. The blank heads have faces stamped onto them by a machine. The next step is to add bodies and have a design stamped on them. From there, arms are added which are followed by hands. The legs are added next but first are assembled by the machine. The pieces are then sorted and packaged.
Here are some interesting stats:
- 23,000 heads are printed per hour.
- 8000 bodies are assembled per hour
- 4 legs are assembled each second
- Over half a billion Minifigures are produced every year.
Final Thoughts
The manufacturing process of LEGO bricks is both complex and fascinating, with each brick requiring a high level of precision to ensure it meets LEGO’s strict quality standards. By understanding this process, we can appreciate the effort that goes into making these iconic plastic building blocks.
From molding to quality control, each step in the process is carefully monitored and inspected. As one of the world’s most beloved toys, LEGO continues to bring joy and creativity to children all over the world.